البحوثوالتنمية
ويركزمعهد بحوثالعامة لليمينغ الصناعة الثقيلةفي مجال البحوث وتطوير التكنولوجيا المتقدمة والمنتجات الموجهة لصالح العملاء، فضلا عن بناءالقدرة التنافسية الجوهريةليجعل يمينغالصناعة الثقيلةرائدةفي هذه الصناعة.من خلال توفيرنتائج البحوثالأساسية، ويدعم المعهديمينغالصناعة الثقيلةالتكنولوجيا والمنتجات لتكون أعلىمنهافي العالمالقائمة.
معهد بحوثالعامة لليمينغ الصناعة الثقيلةهيقسم البحث والتطويرالأوليةللبحوثالتقنيةوالإدارة التقنية. وهي مسؤولة عنتطوير التكنولوجياالمطبقة علىيمينغجميع المنتجات، وإجراء البحوث الفنيةمقدمةعلى المنتجات الجديدةووضعالمعايير؛البحثالاهتزاز، والأثر، والضوضاء، والتكنولوجيا الهيدروليكية، والمطابقة الطاقةوتوفير الطاقة، والمواد الجديدة، وأنظمة التحكم، وخلق تكنولوجياتمبتكرة ومنتجاتحمليوبناءمنصة علىشبكة خاصةوعامةللتجاربوالاختباراتوذلك لتبادل التجربةالعامة ونتائج الاختبار.
محطة الكسارة المتنقلة
مصنع طحن الصناعية
معدات الرمال
اترك رسالة
أشكركم على اهتمامكم في شركة لي منغ للصناعة الثقيلة. يرجى ملء استمارة 'معلومات تحقيق'، أو استخدام أي الأساليب أدناه للحصول على اتصال معنا.
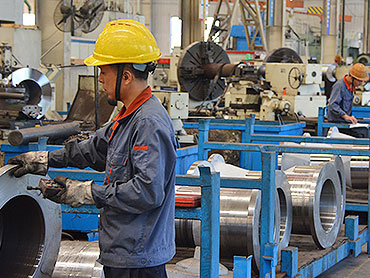
لى مينغ للصناعات الثقيلة وقد القى دائما المعدات المناسبة بالسعر المناسب. لى مينغ للخدمات المالية توفر مجموعة متنوعة من حلول التمويل المصممة خصيصا وترتيبات الشحن في جميع أنحاء العالم لعملائنا. يرجى مراسلتنا مع متطلبات محددة حتى يتسنى لنا أن تشير الخيارات الأكثر جدوى لنقل البضائع الخاصة بك.
سوف لى مينغ للصناعات الثقيلة تدريب مشغلي الخاص، وتوفير المتابعة مرة لاستعراض واستخدام المعدات، والمشورة بشأن الاستخدام الأمثل للأجزاء ارتداء.
معالجة: رقم 169 الطريقة 'كه شيويه' بمنطقة تنمية صناعية عالية وجديدةالتكنولوجيا الوطنية في مدينة تشنغتشو
729041164@qq.com
a typical plan of an iron ore beneficiation process
Iron ore beneficiation: an overview - ScienceDirect
2023year1month1day This chapter briefly discusses the current scenario of the iron ore resources in India, iron ore mining methodology, beneficiation technique, and the current operating practices for achieving sustainable growth in the iron and steel industry.
دردشة على الإنترنتIron Ore Processing: From Extraction to Manufacturing
2024year4month26day 1. Exploration is the process of locating and evaluating potential iron ore reserves. It involves a combination of geological surveys, remote sensing techniques,
دردشة على الإنترنتIron ore beneficiation: an overview - ResearchGate
2023year1month1day The first four variants form typical high-grade run-of-mines (ROMs) (hard, soft and powdery iron ore variants, e.g., ROM-HIO, ROM-SSIO, and ROM-PBD,
دردشة على الإنترنتOre Beneficiation - an overview ScienceDirect Topics
To evaluate an iron ore resource, develop processing routines for iron ore beneficiation, and understand the behavior of the ore during such processing, extensive mineralogical
دردشة على الإنترنتExisting and New Processes for Beneficiation of Indian Iron
2020year2month8day The present communication discusses the beneficiation practices in the Indian context and the recent developments in alternative processing technologies such
دردشة على الإنترنتDriving investments in ore beneficiation and scrap
2021year5month20day This paper addresses the need for investments in ore beneficiation and scrap upgrading in the decades to come in order to meet demands on mitigating emissions of greenhouse gases as discussed at
دردشة على الإنترنتSGS MINERALS SERVICES – T3 SGS 960 11-2009
2023year6month28day Since all iron ore deposits have unique mineralogy, the beneficiation process is specific to each deposit. Separation of certain minerals can be efficiently
دردشة على الإنترنتYour iron ore beneficiation solutions - downergroup
2017year10month24day Our testing uses state‐of‐the‐art iron ore beneficiation equipment for crushing, grinding, classification, gravity and electrostatic separation as well as high and
دردشة على الإنترنتTowards a Sustainable and Enhanced Iron Ore Recovery: Bio-beneficiation ...
2024year3month16day Bio-beneficiation of iron ore potentially offers a relatively energy-efficient, cost-effective, and environmentally friendly method of maximum iron ore recovery.
دردشة على الإنترنتDry beneficiation of iron ore - Mineral Processing
3 Technologies for iron ore beneficiation. Depending on iron content, beneficiation of iron ore for sale is a relatively simple to complex process. In Fig. 3, the typical beneficiation of the
دردشة على الإنترنتBeneficiation - an overview ScienceDirect Topics
11.5.3.1 Beneficiation. Mineral beneficiation begins with crushing and grinding of mined ore for near-complete separation of ore and gangue minerals as well as between ore minerals. Each processing step is designed to increase the grade (concentration) of the valuable components of the original ore.
دردشة على الإنترنتYour iron ore beneficiation solutions - downergroup
2017year10month24day Wright iron ore mine in Canada. In 2011, we delivered 5,760 spiral starts and in 2014 we delivered an additional 2,688 iron ore spiral starts to the mine. These represented the largest delivery of iron ore spirals to any one mine site. To meet Mont Wright’s specific beneficiation requirements, we embarked on an extensive research
دردشة على الإنترنتA critical review on metallurgical recovery of iron from iron ore ...
2024year4month1day Fig. 2 illustrates the iron ore beneficiation process, particularly magnetic separation, resulting in the generation of inevitable tailings. Due to the characteristics of iron ores and the conditions during beneficiation, it is inevitable that approximately 2.5–3 tons of IOTs are generated for every 1 ton of iron ore concentrate produced [7].In 2019, the
دردشة على الإنترنتIron ore beneficiation: an overview - ScienceDirect
2023year1month1day At the current rate of GDP growth, this demand will increase and reach up to 300 MT by 2030. Yet, India’s per capita consumption would reach only 160–180 kg (currently approximately 69 kg), which will be lower than the current global average of 208 kg. Hence, to meet the growing steel demand, the demand for iron ore is also increasing.
دردشة على الإنترنت22.4: Beneficiation - Chemistry LibreTexts
Beneficiation may involve physical or chemical processes. Often, as in the case of panning for gold, the desired ore or metal is denser than the gangue. The latter can be suspended in a stream of water and flushed away. The iron ore magnetite, Fe 3 O 4, is ferrimagnetic. It can be separated from abundant deposits of taconite by grinding to a ...
دردشة على الإنترنتTowards a Sustainable and Enhanced Iron Ore Recovery: Bio-beneficiation ...
2024year3month16day Iron ore is essential in steel making; however, high-grade ores have diminished, making low-grade ores inevitable. These low-grade iron ores need further beneficiation to upgrade the iron content. Currently, traditional physical and chemical methods are utilized and are not environmentally friendly. Bio-beneficiation techniques
دردشة على الإنترنتIron Ore Beneficiation Process - 911 Metallurgist
2017year4month27day Iron Ore Beneficiation Process. Previous. ... The average capacity is nearly 400 tons of crude ore per hour per unit, the maximum being 900 tons. The largest tonnage washed in one season of six months was over 4,000,000 tons of crude ore. The mill can not be operated in freezing weather, and its operating season coincides with the ore-shipping ...
دردشة على الإنترنتBENEFICIATION OF IRON ORE - National Institute of
2014year7month28day silica in iron ore leading to slime generation which are disposed of in tailing ponds. Slime in these tailing ponds contains iron values in the range of 45-60%. Appropriate beneficiation process has to be advanced to reduce the waste generation in mines and for the sustainable growth of the iron ore industry some.
دردشة على الإنترنتChromite ore beneficiation: prospects and challenges
2023year1month1day The average content of the ore is 26% Cr 2 O 3 and the Cr/Fe ratio is 1.55. The Kemi chromium mine is an open-pit mine with a waste rock to ore ratio of 5.5:1. At Kemi, the ore from the mine contains 11% iron and 25.5% Cr 2 O 3. After beneficiation, the concentrate contains between 35% Cr 2 O 3 in the coarse fraction (lumps) and 44% of Cr
دردشة على الإنترنتA Study on High-Grade Iron ore Beneficiation to Reduce
2020year5month21day Iron ore pellets are largely characterized by inherent physical and chemical properties of the ore. Alumina and silica play important roles in determining the productivity of a Blast Furnace. On average, one percent increase in iron content improves productivity by 2% and reduces coke consumption by 1%. Therefore higher iron ore feed content to
دردشة على الإنترنتRecent process developments in beneficiation and
2024year4month1day The proven resource reserves include 35 million tons REO (average grade = 6 wt%), 1400 million tons iron ore, 100 million tons fluorite, and 3.2 million tons Nb 2 O 5. The ratio of bastnaesite to monazite in the deposit is approximately 3:1, and REEs are recycled from iron ore processing tailings. 42 , 43 There are three mining areas in the ...
دردشة على الإنترنتAdvancing Iron Ore Beneficiation: Exploring Cutting-Edge
2024year5month2day The evolution of iron ore beneficiation process technology underscores the industry’s commitment to innovation and sustainability, driving continuous improvement in ore processing efficiency and ...
دردشة على الإنترنتChrome ore beneficiation challenges opportunities – A
2011year4month1day Review of the research works. The critical issues related to the chromite process plants investigated by various researchers have been categorized as: 5.1. Reducing the tailing losses (9–20% Cr 2 O 3 ). 5.2. Beneficiation of low and sub-grade chromite ore (10–30% Cr 2 O 3 ). 5.3.
دردشة على الإنترنتIron Ore Processing: From Extraction to Manufacturing
2024year4month26day The beneficiation process aims to increase the iron content and reduce impurities in the ore, resulting in a higher-quality concentrate suitable for further processing and utilization. The specific beneficiation method employed depends on factors such as the mineralogy of the ore, the presence of specific impurities, and the desired iron content.
دردشة على الإنترنت(PDF) Iron Ore Pelletizing Process: An Overview - ResearchGate
2018year7month11day The iron ore pelletizing process consists of three main steps: 1. Pelletizing feed preparation and mixing: the raw material (iron ore concentrate, additives. — anthracite, dolomite — and ...
دردشة على الإنترنتTreatment of iron ore beneficiation plant process water by ...
2021year1month1day Table 2 shows the concentrations of various metal ions and other water quality parameters present in process water collected from iron ore beneficiation plant followed by settling and filtration. It is observed from the results that the concentration of total Fe, Cr, Pb, Mn and turbidity are found to be 115.24 mg/L, 7.10 mg/L, 2.68 mg/L, 0.96
دردشة على الإنترنتIron Ore Beneficiation Plant - JXSC Machinery - Mineral
2024year5month24day Iron ore beneficiation is mainly a process of separating valuable minerals and iron minerals from ores to extract high-quality iron ore. The iron ore process mainly includes crushing, grinding, washing, beneficiation, dewatering, etc. . Magnetite Beneficiation: The main iron mineral contained in magnetite is iron tetroxide (Fe3O4).
دردشة على الإنترنتHow to Process Copper Ore: Beneficiation Methods and Equipment
2023year3month13day Before the beneficiation of copper ores, crushing and grinding are required. The bulk ores are crushed to about 12cm by a jaw crusher or a cone crusher. Then the crushed materials are sent to the grinding equipment, and the final particle size of the copper ore is reduced to 0.15-0.2mm. Copper ore crushing process. 1.
دردشة على الإنترنتEquipment Configuration Plan and Process of Iron Ore
In the beneficiation process of gold mines, CIP and CIL beneficiation processes are common process technologies. Although they are all 3 min read Feb 11, 2024
دردشة على الإنترنت
شاهد المزيد
- حجر محطم التجارية الصغيرة للبيع
- آلة معالجة النيس للبيع
- قطعات یدکی آسیاب هند
- صناعة الصين الصين ماكينات صناعة الفحم
- آلة طحن كربونات الكالسيوم في تركيا
- مصنعي مطحنة الكرة العمودية
- كسارة الصخور plantportable
- كسارة الفحم للبيع في سلوفاكيا
- حار بيع كسارة تأثير رمح عمودي أعلى في الصين
- كسارة الجرانيت في المملكة العربية السعودية
- مناجم الموليبدينوم في الفلبين
- ذروة خام الحديد سحق الآلات فحص
- بيع معدات سحق الذهب متوسطة الحجم
- غربال پر جنب و جوش
- آلة صنع الرمل المستعملة للبيع كوريا